1. Introduction to Silicon Carbide Seal Faces
Silicon carbide seal faces are designed to provide reliable and efficient sealing in extreme conditions. SiC is a compound of silicon and carbon, known for its exceptional hardness, thermal conductivity, and resistance to wear and corrosion. These attributes make SiC an excellent material for sealing applications where longevity and performance are critical.
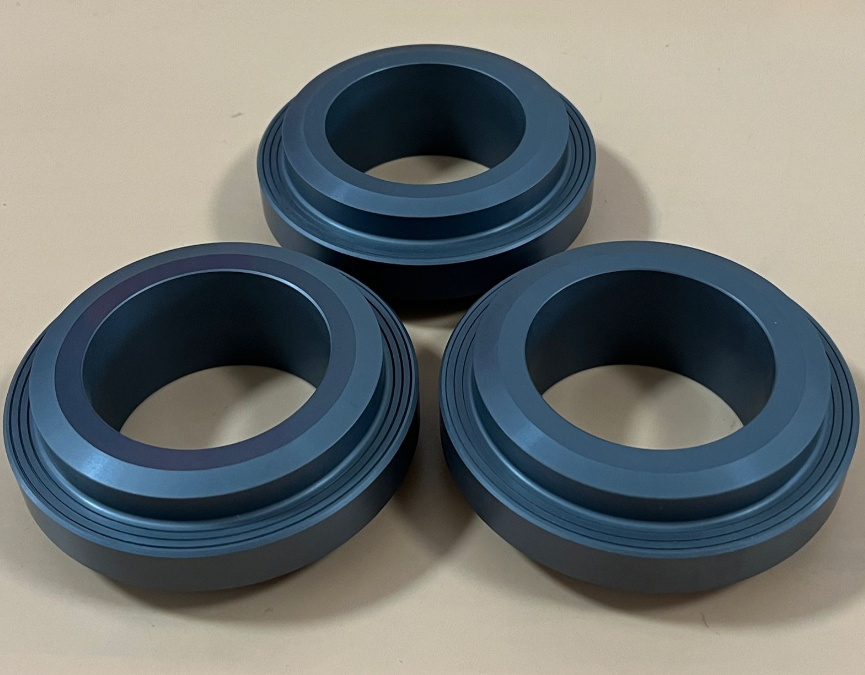
2. Benefits of Silicon Carbide Seal Faces
Durability: SiC is one of the hardest materials available, ensuring long-lasting performance and reduced maintenance.
Thermal Stability: High thermal conductivity and low thermal expansion make SiC suitable for high-temperature applications.
Wear Resistance: SiC's hardness provides excellent resistance to wear and abrasion, extending the life of the seal.
Corrosion Resistance: SiC is chemically inert, making it resistant to a wide range of chemicals and corrosive environments.
Low Friction: The smooth surface of SiC reduces friction, enhancing the efficiency of sealing applications.
3. Applications of Silicon Carbide Seal Faces
Chemical Processing: SiC seals are used in pumps, compressors, and mixers where chemical resistance is vital.
Oil and Gas: In drilling and extraction operations, SiC seals ensure reliability and safety in extreme conditions.
Industrial Machinery: High-temperature and high-pressure environments benefit from the durability of SiC seals.
Aerospace: SiC seals are used in engines and other components where high performance is essential.
4. Production Process of Silicon Carbide Seal Faces
The production of silicon carbide seal faces involves several key steps:
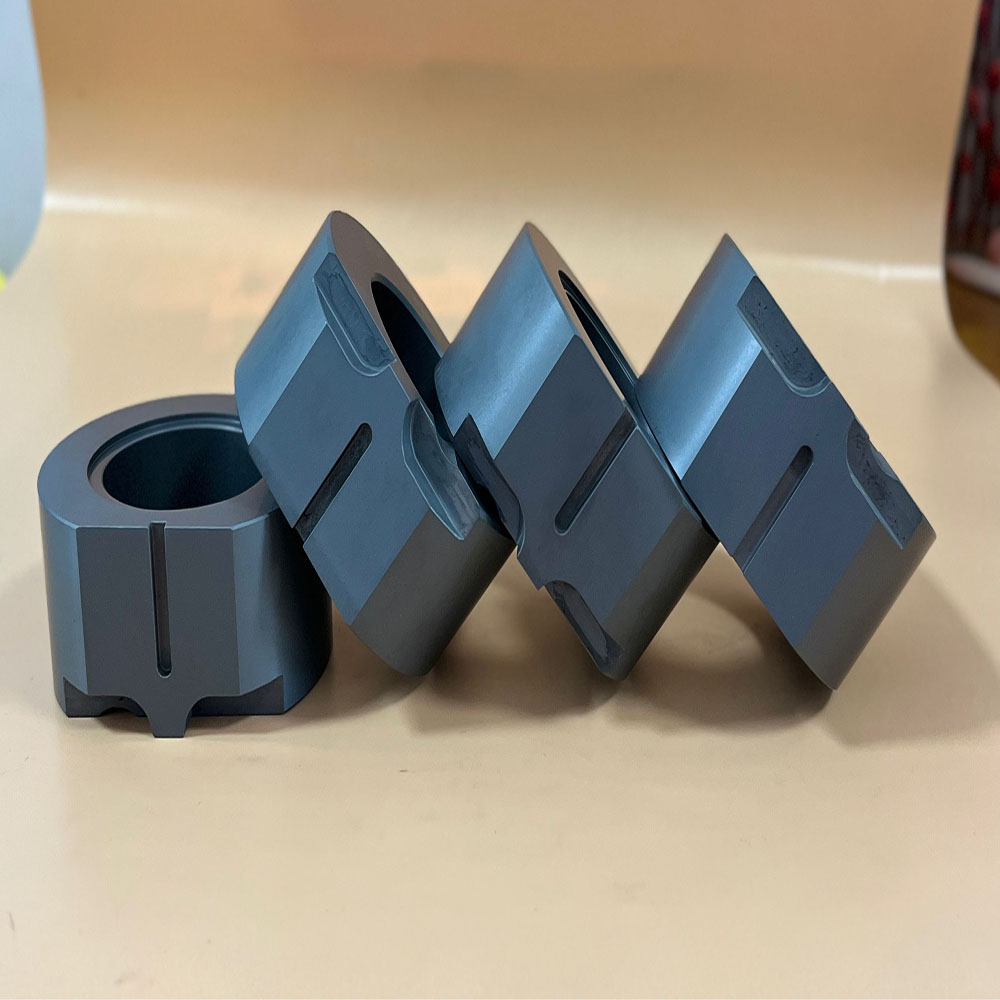
Raw Material Preparation: High-purity silicon and carbon sources are selected to ensure the quality of the final product.
Mixing and Forming: The raw materials are mixed and formed into the desired shape using methods such as pressing or extrusion.
Sintering: The formed parts are heated to high temperatures in a controlled atmosphere to facilitate the bonding of silicon and carbon atoms, creating a dense and hard SiC structure.
Machining: After sintering, the SiC parts are machined to precise dimensions and surface finishes using diamond tools, as SiC's hardness requires specialized equipment.
Quality Control: The finished seal faces undergo rigorous quality control tests to ensure they meet the required specifications for hardness, density, and surface finish.
Final Inspection and Packaging: Each seal face is inspected for any defects, then packaged carefully to prevent damage during transportation.
5. Conclusion
Silicon carbide seal faces represent a significant advancement in sealing technology, offering superior performance in demanding applications. Their unique properties, such as high hardness, thermal stability, and resistance to wear and corrosion, make them an indispensable component in various industries. Understanding the production process of sic seal faces highlights the precision and expertise required to produce these high-performance seals.
By leveraging the benefits of silicon carbide, industries can achieve greater efficiency, reliability, and longevity in their operations, ensuring continued success in even the most challenging environments.
This overview should provide a comprehensive introduction to silicon carbide seal faces, their advantages, applications, and the production process. If you need more specific details or further customization, feel free to let us know!