1. Direct Sintered Silicon Carbide (SSiC):
- SSiC is produced by sintering silicon carbide powder with various additives at high temperatures (typically above 2000°C) and pressures to form a dense, high-strength ceramic.
- It has excellent mechanical properties, high hardness, and good thermal conductivity.
- SSiC is chemically inert and highly resistant to corrosion, making it suitable for applications in harsh environments such as chemical processing, semiconductor manufacturing, and aerospace.
2. Reaction Bonded Silicon Carbide (RBSC):
- RBSC is formed by infiltrating porous silicon carbide preforms with liquid silicon, which then reacts with the carbon in the preform to form additional silicon carbide.
- This process creates a composite material with a network of silicon carbide grains bonded together by residual silicon.
- RBSC typically has lower density and mechanical strength compared to SSiC but exhibits better thermal shock resistance and can be manufactured into complex shapes more easily.
- It is often used in applications requiring thermal stability and wear resistance, such as kiln furniture, burner nozzles, and mechanical seals.
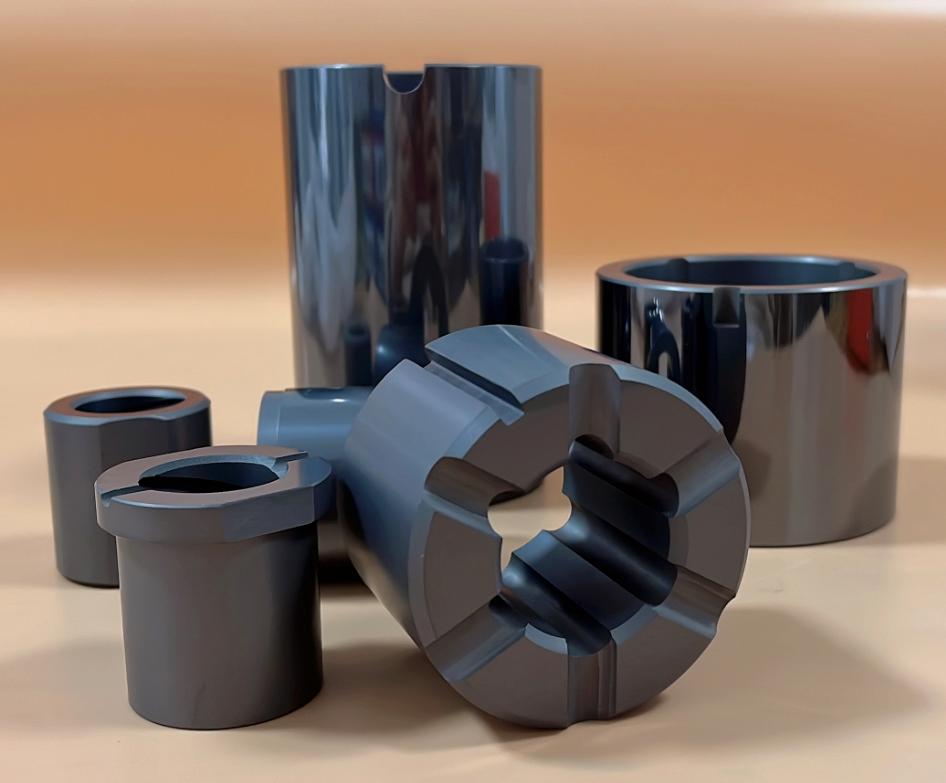
In summary, SSiC offers superior mechanical properties and chemical resistance, while RBSC provides better thermal shock resistance and is more suitable for intricate shapes and lower-cost manufacturing. The choice between the two depends on the specific requirements of the application.